Kompresory to urządzenia mechaniczne, które mają na celu zwiększenie ciśnienia gazu poprzez zmniejszenie jego objętości. Działają na zasadzie zasysania powietrza lub innego gazu, a następnie jego sprężania, co prowadzi do wzrostu ciśnienia. Istnieje wiele rodzajów kompresorów, w tym kompresory tłokowe, śrubowe oraz wirnikowe, które różnią się między sobą konstrukcją oraz zastosowaniem. Kompresory tłokowe wykorzystują ruch posuwisto-zwrotny tłoka do sprężania gazu, podczas gdy kompresory śrubowe działają na zasadzie obracających się wirników, które zmniejszają objętość gazu. W przypadku kompresorów wirnikowych wykorzystuje się wirniki o specjalnym kształcie, które również sprężają gaz. Kompresory znajdują zastosowanie w wielu dziedzinach przemysłu, od produkcji energii po chłodnictwo i klimatyzację. Dzięki swojej funkcji sprężania gazu są niezbędne w procesach technologicznych, gdzie wymagane jest dostarczenie sprężonego powietrza lub innych gazów pod wysokim ciśnieniem.
Jakie są różne typy kompresorów i ich zastosowania?
Na rynku dostępnych jest wiele różnych typów kompresorów, które różnią się zarówno konstrukcją, jak i zastosowaniem. Kompresory tłokowe są jednymi z najpopularniejszych modeli i znajdują szerokie zastosowanie w warsztatach oraz małych zakładach przemysłowych. Charakteryzują się one prostą budową oraz stosunkowo niskimi kosztami eksploatacji. Z kolei kompresory śrubowe są bardziej zaawansowane technologicznie i idealnie nadają się do dużych zakładów produkcyjnych, gdzie wymagane jest ciągłe dostarczanie sprężonego powietrza. Dzięki swojej wydajności i niezawodności często stosowane są w przemyśle motoryzacyjnym oraz budowlanym. Kompresory wirnikowe z kolei znajdują zastosowanie w branży lotniczej oraz w systemach chłodniczych ze względu na swoją wysoką efektywność energetyczną. Warto również wspomnieć o kompresorach przenośnych, które cieszą się dużą popularnością wśród majsterkowiczów i profesjonalistów zajmujących się pracami remontowymi.
Jakie są kluczowe zalety korzystania z kompresorów?
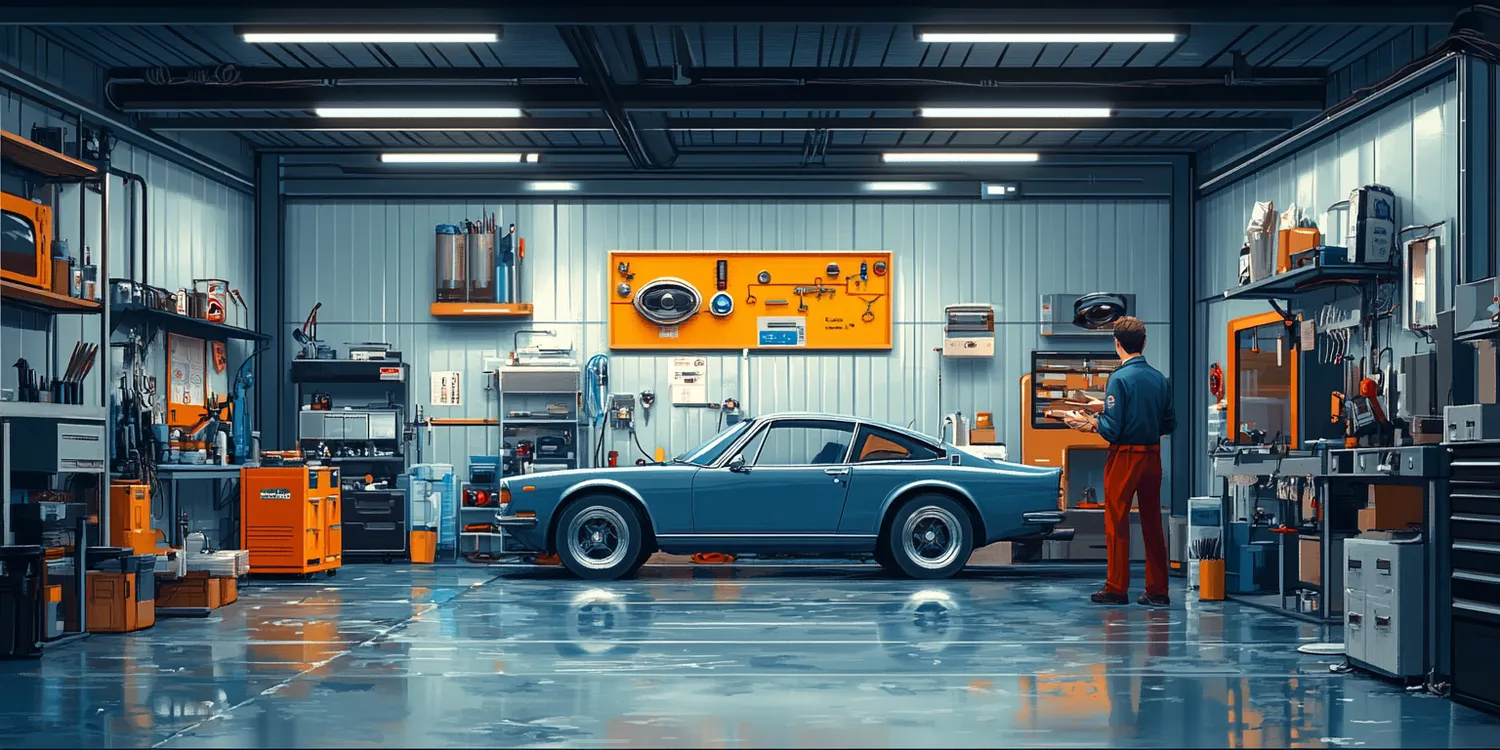
Kompresory co to jest?
Korzystanie z kompresorów niesie ze sobą wiele korzyści zarówno dla przemysłu, jak i użytkowników indywidualnych. Przede wszystkim kompresory pozwalają na efektywne wykorzystanie energii poprzez sprężanie gazu, co umożliwia dostarczanie go pod wysokim ciśnieniem do różnych aplikacji. Dzięki temu możliwe jest zasilanie narzędzi pneumatycznych, takich jak wkrętarki czy młoty udarowe, co znacznie zwiększa ich wydajność i komfort pracy. Ponadto sprężone powietrze może być wykorzystywane do czyszczenia powierzchni czy też jako medium transportowe w systemach pneumatycznych. Kolejną zaletą jest oszczędność miejsca – nowoczesne kompresory zajmują niewiele przestrzeni, co czyni je idealnym rozwiązaniem dla małych warsztatów czy domowych garaży. Warto również zwrócić uwagę na ich trwałość oraz niskie koszty eksploatacji, co czyni je opłacalną inwestycją na długie lata.
Jakie są najczęstsze problemy związane z kompresorami?
Mimo licznych zalet korzystania z kompresorów mogą występować pewne problemy związane z ich eksploatacją i konserwacją. Jednym z najczęstszych problemów jest nadmierna ilość wilgoci w sprężonym powietrzu, co może prowadzić do korozji elementów układu pneumatycznego oraz obniżenia wydajności narzędzi pneumatycznych. Aby temu zapobiec, ważne jest regularne sprawdzanie filtrów oraz stosowanie osuszaczy powietrza. Innym problemem mogą być wycieki powietrza, które mogą wynikać z uszkodzeń uszczelek lub połączeń w układzie pneumatycznym. Regularna kontrola stanu technicznego urządzenia oraz jego komponentów pozwala na szybką identyfikację i usunięcie usterek. Warto również pamiętać o regularnej konserwacji samego kompresora – wymiana oleju oraz czyszczenie filtrów to kluczowe czynności wpływające na jego żywotność i efektywność działania.
Jakie są najważniejsze czynniki przy wyborze kompresora?
Wybór odpowiedniego kompresora jest kluczowy dla efektywności jego działania oraz zadowolenia użytkownika. Przede wszystkim należy zwrócić uwagę na przeznaczenie urządzenia. Inne wymagania będą miały warsztaty rzemieślnicze, a inne zakłady przemysłowe. W przypadku małych warsztatów idealnym rozwiązaniem mogą być kompresory tłokowe, które charakteryzują się niską ceną oraz prostą obsługą. Natomiast w większych zakładach produkcyjnych warto rozważyć inwestycję w kompresory śrubowe, które zapewniają wyższą wydajność oraz ciągłość pracy. Kolejnym istotnym czynnikiem jest wydajność kompresora, mierzona w litrach na minutę lub metrach sześciennych na godzinę. Warto dopasować tę wartość do zapotrzebowania na sprężone powietrze w danym zastosowaniu. Należy również zwrócić uwagę na ciśnienie robocze, które powinno być dostosowane do wymagań narzędzi i urządzeń, które będą zasilane sprężonym powietrzem. Dodatkowo, ważne są aspekty związane z mobilnością kompresora – jeśli planujemy korzystać z niego w różnych miejscach, warto wybrać model przenośny, który będzie łatwy do transportu.
Jakie są najczęstsze zastosowania kompresorów w przemyśle?
Kompresory znajdują szerokie zastosowanie w różnych branżach przemysłu, co sprawia, że są niezwykle wszechstronnymi urządzeniami. W przemyśle budowlanym sprężone powietrze jest wykorzystywane do zasilania narzędzi pneumatycznych, takich jak młoty udarowe czy wkrętarki, co znacznie zwiększa efektywność pracy. W branży motoryzacyjnej kompresory służą do pompowania opon oraz zasilania systemów pneumatycznych w pojazdach. W przemyśle spożywczym sprężone powietrze jest wykorzystywane do pakowania produktów oraz utrzymania czystości w procesach produkcyjnych. Kompresory odgrywają również kluczową rolę w systemach chłodniczych i klimatyzacyjnych, gdzie sprężone powietrze jest niezbędne do obiegu czynnika chłodniczego. W sektorze medycznym kompresory są używane do dostarczania sprężonego powietrza do urządzeń medycznych, takich jak respiratory czy inhalatory. Warto również wspomnieć o zastosowaniach komercyjnych – wiele firm korzysta z kompresorów do czyszczenia sprzętu biurowego oraz utrzymania porządku w przestrzeni roboczej.
Jak dbać o kompresor, aby działał sprawnie przez lata?
Aby kompresor działał sprawnie przez długi czas, konieczna jest regularna konserwacja i dbanie o jego stan techniczny. Kluczowym elementem jest regularna wymiana oleju silnikowego oraz filtrów powietrza, co pozwala na utrzymanie optymalnej wydajności urządzenia. Należy również regularnie sprawdzać poziom oleju oraz uzupełniać go w razie potrzeby. Ważne jest także monitorowanie stanu uszczelek i połączeń – wszelkie nieszczelności mogą prowadzić do strat energii oraz obniżenia efektywności działania kompresora. Kolejnym krokiem jest kontrola układu chłodzenia – przegrzewanie się urządzenia może prowadzić do jego uszkodzenia, dlatego warto regularnie czyścić kratki wentylacyjne oraz sprawdzać działanie wentylatorów chłodzących. Dobrą praktyką jest także przeprowadzanie okresowych przeglądów technicznych przez specjalistów, którzy mogą zidentyfikować ewentualne problemy zanim staną się one poważniejsze.
Jakie są nowoczesne technologie stosowane w kompresorach?
W ostatnich latach rozwój technologii wpłynął na konstrukcję i funkcjonalność kompresorów, co pozwoliło na zwiększenie ich wydajności oraz zmniejszenie kosztów eksploatacji. Nowoczesne kompresory często wyposażane są w zaawansowane systemy sterowania elektronicznego, które umożliwiają precyzyjne zarządzanie pracą urządzenia oraz monitorowanie jego parametrów w czasie rzeczywistym. Dzięki temu możliwe jest dostosowanie pracy kompresora do aktualnego zapotrzebowania na sprężone powietrze, co przekłada się na oszczędność energii i niższe koszty eksploatacji. Ponadto wiele nowoczesnych modeli wyposażonych jest w systemy odzysku ciepła, które pozwalają na wykorzystanie energii cieplnej generowanej podczas pracy kompresora do podgrzewania wody lub innych procesów technologicznych. Warto również zwrócić uwagę na rozwój technologii bezolejowej – takie kompresory eliminują potrzebę stosowania oleju smarowego, co przekłada się na czystsze powietrze i mniejsze ryzyko kontaminacji sprężonego gazu.
Jakie są różnice między kompresorami olejowymi a bezolejowymi?
Kompresory olejowe i bezolejowe różnią się przede wszystkim sposobem smarowania oraz zastosowaniem. Kompresory olejowe wykorzystują olej smarowy do redukcji tarcia między ruchomymi częściami silnika i tłoka, co przekłada się na ich dłuższą żywotność oraz większą wydajność. Są one idealnym rozwiązaniem dla aplikacji przemysłowych wymagających dużej ilości sprężonego powietrza pod wysokim ciśnieniem. Z drugiej strony kompresory bezolejowe nie wymagają stosowania oleju smarowego, co eliminuje ryzyko kontaminacji sprężonego powietrza olejem lub innymi substancjami chemicznymi. Dlatego też są one często wykorzystywane w branżach spożywczej i farmaceutycznej, gdzie czystość sprężonego powietrza ma kluczowe znaczenie. Warto jednak zauważyć, że kompresory bezolejowe mają tendencję do szybszego zużywania się ze względu na brak smarowania, co może prowadzić do konieczności częstszej wymiany komponentów lub całego urządzenia.
Jakie są przyszłe trendy rozwoju technologii kompresorowej?
Przemysłowa technologia kompresorowa stale ewoluuje i dostosowuje się do zmieniających się potrzeb rynku oraz rosnącej świadomości ekologicznej użytkowników. Jednym z kluczowych trendów jest rozwój energooszczędnych rozwiązań mających na celu minimalizację zużycia energii podczas pracy kompresorów. Producenci coraz częściej inwestują w technologie automatyzacji i inteligentnego zarządzania pracą urządzeń, co pozwala na optymalizację ich wydajności oraz redukcję kosztów eksploatacyjnych. Również rosnące zainteresowanie odnawialnymi źródłami energii wpływa na rozwój nowych modeli kompresorów zasilanych energią słoneczną czy wiatrową.